Why ERP Alone Can’t Handle Real-Time Production Disruptions
- Matt Ulepic
- May 29
- 4 min read
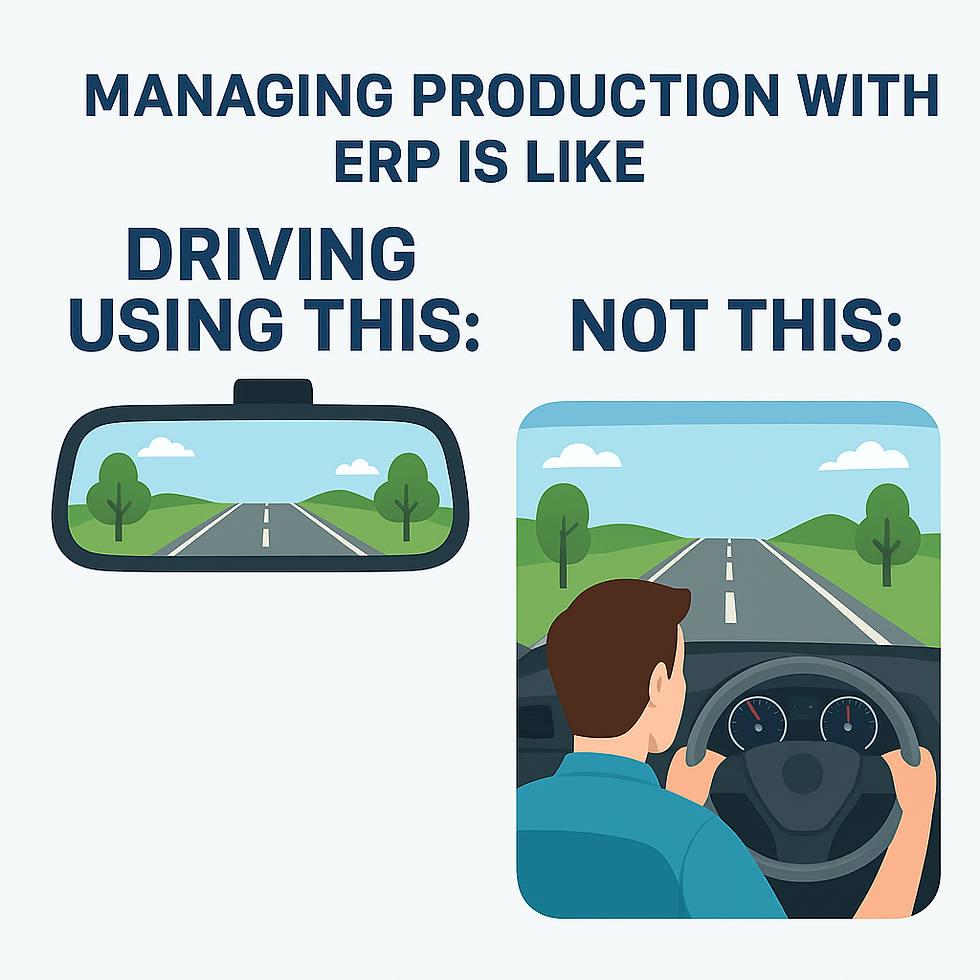
“We already have ERP.”
It’s a common response we hear from manufacturers when the topic of real-time machine tracking comes up. And it makes sense on the surface—Enterprise Resource Planning systems are a core part of how many manufacturers operate. They help manage everything from purchasing to production planning, inventory, costing, and even compliance.
But there’s a fundamental misunderstanding baked into that answer.
ERP systems are not designed to manage what’s happening on the shop floor right now.
They’re excellent at reporting what happened, and good at helping you plan what should happen. But when it comes to dealing with what is happening—right now, in real-time—they fall short.
And when it comes to production disruptions, delays, and downtime, that gap can cost you.
The Rearview Mirror Problem
Let’s use a simple analogy: trying to manage real-time production disruptions with ERP is like trying to drive your car by looking only in the rearview mirror.
ERP systems are built around data that has already been entered, processed, and committed—whether that’s through manual entry by operators or through batch imports from machines at the end of the day. By the time your ERP reports on a machine issue, it’s often too late to take corrective action.
For example:
A shift that underperformed last night? You won’t know until the report shows up this morning.
A bottleneck that caused unexpected downtime? ERP may reflect the delay eventually, but it won’t show why it happened—or whether it’s still happening.
This delay in visibility leads to reactionary decision-making. You’re constantly playing catch-up, trying to piece together what went wrong and when, often by interviewing operators or walking the floor with a clipboard. It’s inefficient, and worse—it’s unreliable.
What Real-Time Data Does That ERP Can’t
Real-time machine tracking closes the gap between what’s happening and when you learn about it. It provides live, streaming visibility into your equipment status—so you can take action during the shift, not after it’s over.
Here’s what that looks like in practice:
1. Instant Visibility for Production Leads
Rather than waiting until morning to understand why yesterday’s numbers were low, production leads can see the status of every machine in real-time. If downtime starts creeping up or if a machine is underperforming, they can intervene—whether that means reassigning an operator, adjusting the workflow, or escalating a maintenance issue.
2. Shift-to-Shift Accountability
With real-time dashboards and shift-specific summaries, you can compare performance between teams. If the night shift consistently underperforms, it’s easy to see—and even easier to start a data-driven conversation about why. ERP reports may capture the numbers days later, but machine tracking shows the trend as it’s developing.
3. Downtime Classification and Root Cause Insight
ERP systems typically don’t classify downtime unless someone enters a code manually, which often happens long after the fact—if at all. A real-time system like MachineTracking automatically tracks machine state and can even help operators log reasons with a few taps. That means downtime doesn’t just get recorded—it gets explained.
4. Increased Operator Engagement
When operators see their performance in real-time—on dashboards or large displays—they tend to respond. Just like fitness improves when you’re watching the scale, uptime improves when you’re watching the monitors. That visibility drives behavior. ERP systems, on the other hand, are invisible to most operators.
Real-Time Tracking and ERP: Complementary, Not Competitive
It’s important to note: this isn’t about replacing ERP. ERP still plays a vital role in managing business operations. But it was never designed to be a real-time production visibility tool.
Think of ERP as the long-term memory of your business—it records what happened so you can track trends, analyze costs, and plan ahead.
Machine Tracking, on the other hand, is like your nervous system—it tells you what’s happening right now so you can respond and adapt.
Together, these systems complement each other. But expecting ERP to fill both roles is like expecting your accountant to run your production line.
A Real-World Example: Seeing the Night Shift Clearly
We recently worked with a manufacturer who had a solid ERP system and a well-documented workflow. But they had a persistent issue: the night shift was falling short of production goals. The ERP reports showed a dip, but the cause was unclear. Operators blamed the setup from the day shift, maintenance cited tool wear, and management was left guessing.
Once Machine Tracking was installed, the story changed.
They could see:
When the machines started and stopped each shift
How long they were running vs. idle
The precise moments when utilization dropped—and why
Turns out, it wasn’t setup or tools. It was inconsistent operator coverage and missed start times. They addressed the issue quickly—because they finally had the right information at the right time.
Why It Matters Now More Than Ever
In today’s manufacturing environment, margins are tight and customer expectations are high. You don’t have the luxury of waiting for weekly reports to figure out what went wrong. You need tools that give you a live look at your production floor—so you can prevent downtime, not just document it.
And that’s exactly what Machine Tracking does.
You wouldn’t drive your car while looking only in the rearview mirror.
So why run your factory that way?
ERP Can’t Handle Real-Time Production Disruptions
If you’re relying solely on ERP to manage production, you’re missing the opportunity to act in real time. You’re reacting after the fact, not adapting in the moment.
Real-time machine tracking gives your team the visibility they need to keep machines running, shifts productive, and operations on target.
So the next time someone says, “We already have ERP,” ask a simple question:
Can it tell you what’s happening right now?
If the answer is no—it’s time to add a tool that can.
Want to see how Machine Tracking can complement your ERP and boost your uptime?
Schedule a quick demo or reach out to our team—we’d love to show you what real-time really looks like.